Versatile Veneer Production
We offer everything from individual dryer plants with manual feeders, to complete veneer drying lines with automatic feeders, scanners and stacking systems. We supply the wood manufacturing sector with state-of-the-art technology for veneer drying, including the highest possible energy efficiency.
Decorative veneers are sliced and dried in Grenzebach plants all over the world. These veneers are used in the furniture sector, on yachts, in hotels, and for other interior design purposes. Peeled veneers dried on our drying lines are used to make plywood and LVL (laminated veneer lumber).
Get all information
Grenzebach plants are in use for veneer production worldwide.
meters per minute is the stacking speed reached by our stacking and grading systems.
metres in length and 6 decks measures the worldwide longest veneer dryer, made by Grenzebach.
meters is the usual working width of our eight deck dryers.
1977
Formerly Babcock BSH AG
In 1977 the three companies Buettner, Schilde and Haas founded BSH AG, later known as Babcock BSH.
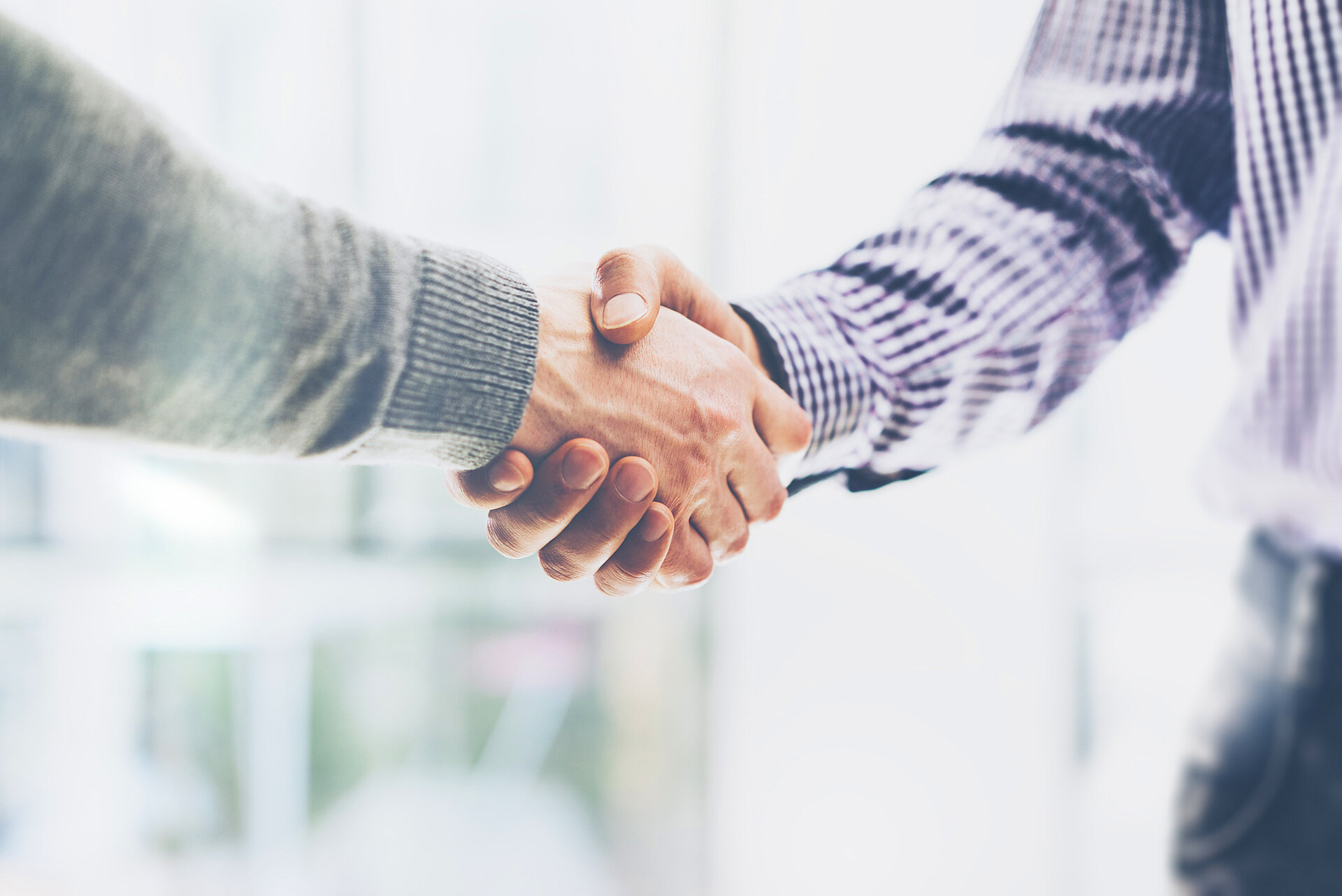
2002
Babcock BSH merged with Grenzebach
In 2002 we acquired Babcock BSH in Bad Hersfeld, Germany. Today Grenzebach bundles worldwide the competencies and state-of-the-art technologies for the building materials sectors.
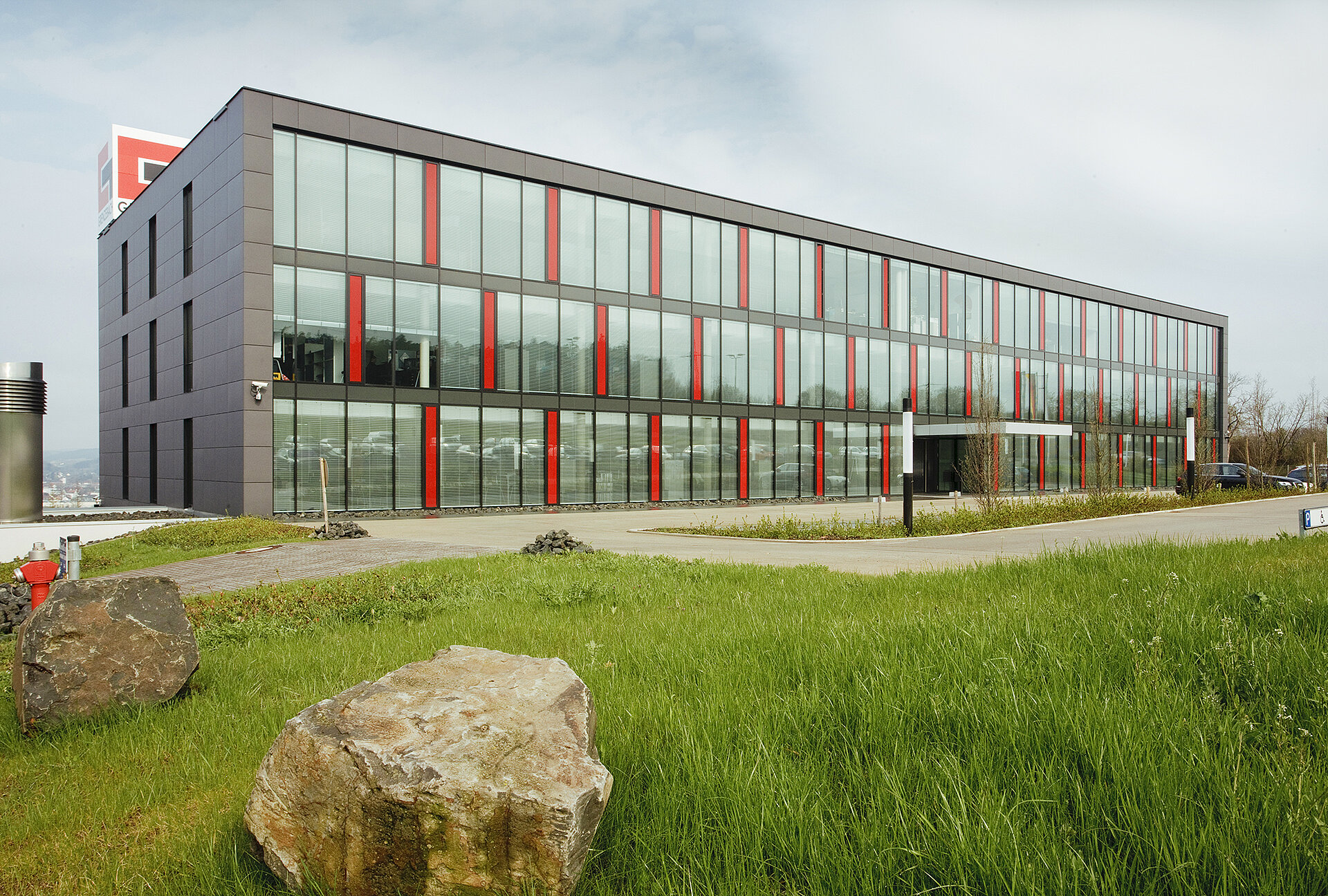
Veneer Drying Technology for Peeled Veneers & Decorative Veneers
Equipment & Highlights
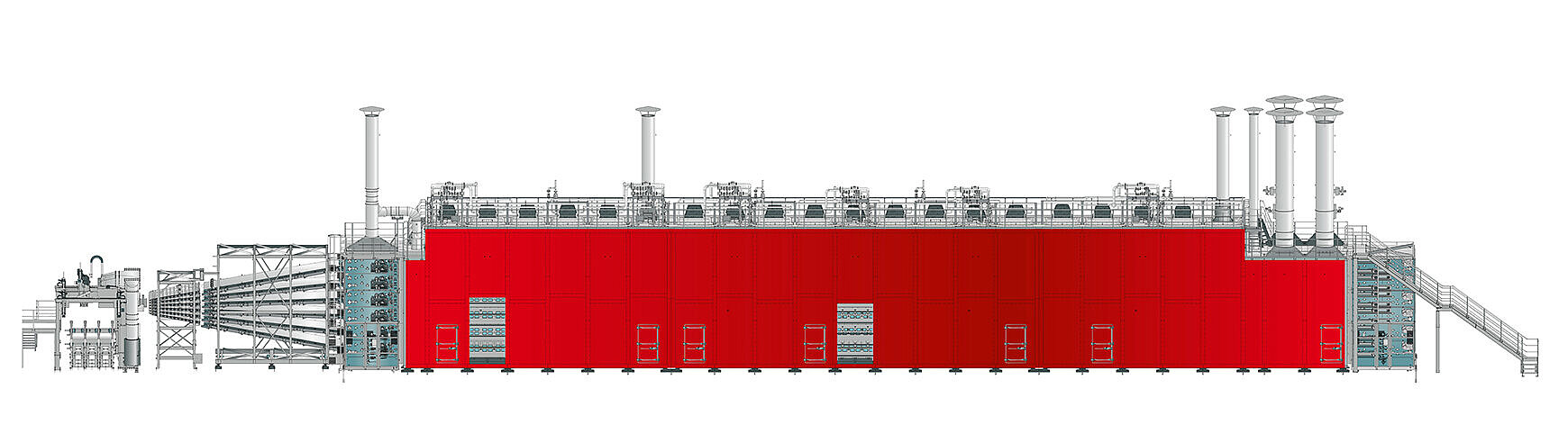
Automatic infeed system with up to 23 cycles/min
Overlapping of the veneer sheets at the infeed to optimize the track load and taking into account the shrinkage of the veneer during drying.
Improved air distribution
Flow-optimized air distribution zones and a better balanced air volume over all decks for best, uniform drying results. The result is a higher drying capacity at lower energy consumption, and a high quality final product.
Modular design
Each modular dryer section is 2.25 m long. These modules are combined to obtain the required dryer length. Four, six or eight deck dryers with a working width of 4 m, 4.8 m, 5 m, 5.8 m and 6.2 m are available.
Special door design
Each aluminized access door extends over an entire section. It can be opened with one hand and features a special door hinge design. Soft bends instead of sharp 90° corners ensure a long lasting and perfect sealing effect.
Sine wave system
The special sine-wave guiding system between carry and cover belt helps to reduce the waviness in particularly wet and difficult to dry veneer species.
Consistent drying
The optimized nozzle boxes with saw tooth tread design guarantee a homogenous distribution of the drying air over the entire width and prevent damage to the veneer sheets.
Improved seal section
End-seal section at the wet end to prevent condensation and carbonization of wood pitch on the dryer walls.
Insulated dryer floor
Insulated floor for highest energy efficiency. No need for special foundations.
Improved end-seal system
End-seal at the dry end to prevent condensation and carbonization of wood pitch on the dryer walls.
Overlapping of the veneer sheets at the infeed to optimize the track load and taking into account the shrinkage of the veneer during drying.
Flow-optimized air distribution zones and a better balanced air volume over all decks for best, uniform drying results. The result is a higher drying capacity at lower energy consumption, and a high quality final product.
Each modular dryer section is 2.25 m long. These modules are combined to obtain the required dryer length. Four, six or eight deck dryers with a working width of 4 m, 4.8 m, 5 m, 5.8 m and 6.2 m are available.
Each aluminized access door extends over an entire section. It can be opened with one hand and features a special door hinge design. Soft bends instead of sharp 90° corners ensure a long lasting and perfect sealing effect.
The special sine-wave guiding system between carry and cover belt helps to reduce the waviness in particularly wet and difficult to dry veneer species.
The optimized nozzle boxes with saw tooth tread design guarantee a homogenous distribution of the drying air over the entire width and prevent damage to the veneer sheets.
End-seal section at the wet end to prevent condensation and carbonization of wood pitch on the dryer walls.
Insulated floor for highest energy efficiency. No need for special foundations.
End-seal at the dry end to prevent condensation and carbonization of wood pitch on the dryer walls.
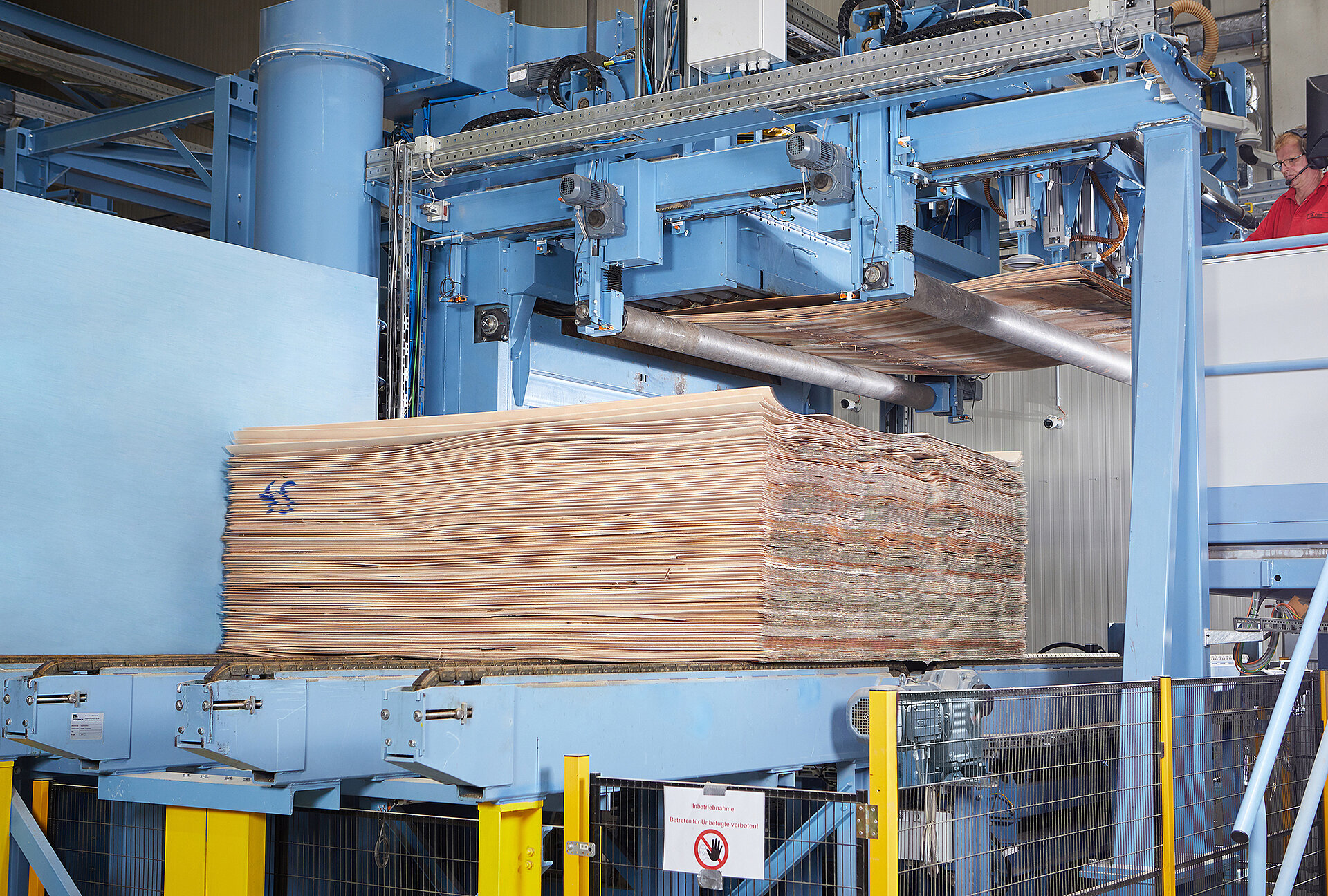
Plant Technologies
Portfolio
Measuring System
Your Benefits at a Glance
Pioneering Technology
Optimized drying process with flow-optimized air distribution and balanced airflow across all decks for more uniform drying results.
Durability
Aluminized sheet metal construction for the entire dryer skin, providing corrosion resistance and long-lasting durability.
Efficient Access
Floating skin-type doors with a special hinge design, easily opened with one hand, featuring durable, flexible stainless steel seals covered with Kevlar®-reinforced fabric.
Superior Insulation
Thick insulation and advanced sealing systems minimize heat loss and ensure rapid, uniform heat-up.
Advanced Airlock Systems
Airlock systems and fresh air preheating devices prevent condensation and resinification, maintaining optimal conditions within the dryer.
Modular Flexibility
Dryer sections are 2.25 m long, allowing for customizable dryer lengths, available in four, six, or eight-deck configurations with various working widths.
Reliability & Quality
Grenzebach’s new generation roller track dryers offer exceptional reliability, minimized downtime, low energy consumption, and superior final product quality. Our partner company Millennium is serving the right solution for your needs on programming and controls.
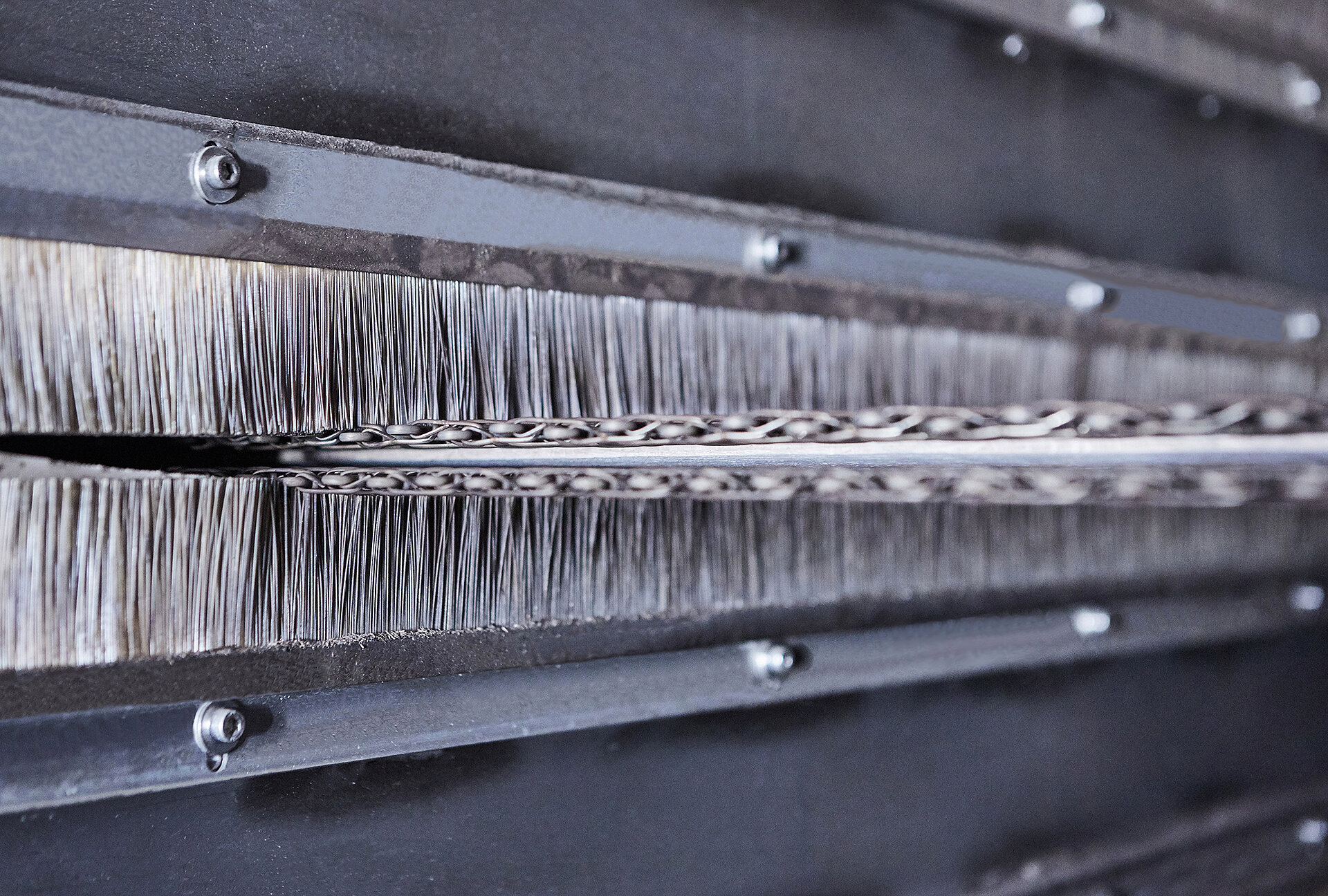
Quality Non-stop
Sine-wave guiding system in the veneer dryer
The unique sine-wave guiding system reduces the waviness of the veneers even when drying wood species with an extremely high moisture content, making handling and processing of the plywood veneers better and easier. The carry and cover belts and the special sine-wave system ensure that the moist veneer sheets, which tend to become wavy, are dried smooth and flat. Belt dryers without sine-wave guiding systems sometimes face the problem of so-called "omega" dry veneers, i.e. deformed sheets that obstruct the run of the sheets and clog up the dryer. Such sheets are not suitable for further processing into plywood or LVL. In the sine-wave belt dryer there are no such stoppages, and waste can be minimized. Not least thanks to the high availability of the system, this also results in a better utilization in downstream production stages.
“We have opted for Grenzebach because their team has a lot of experience in veneer drying. Grenzebach's know-how and service have assisted us with our innovation process. Of course, a number of trial runs were necessary before the optimum was reached, but then drying 3.55 mm beech veneer is not something that can easily be mastered.”

Downloads & Links
More information
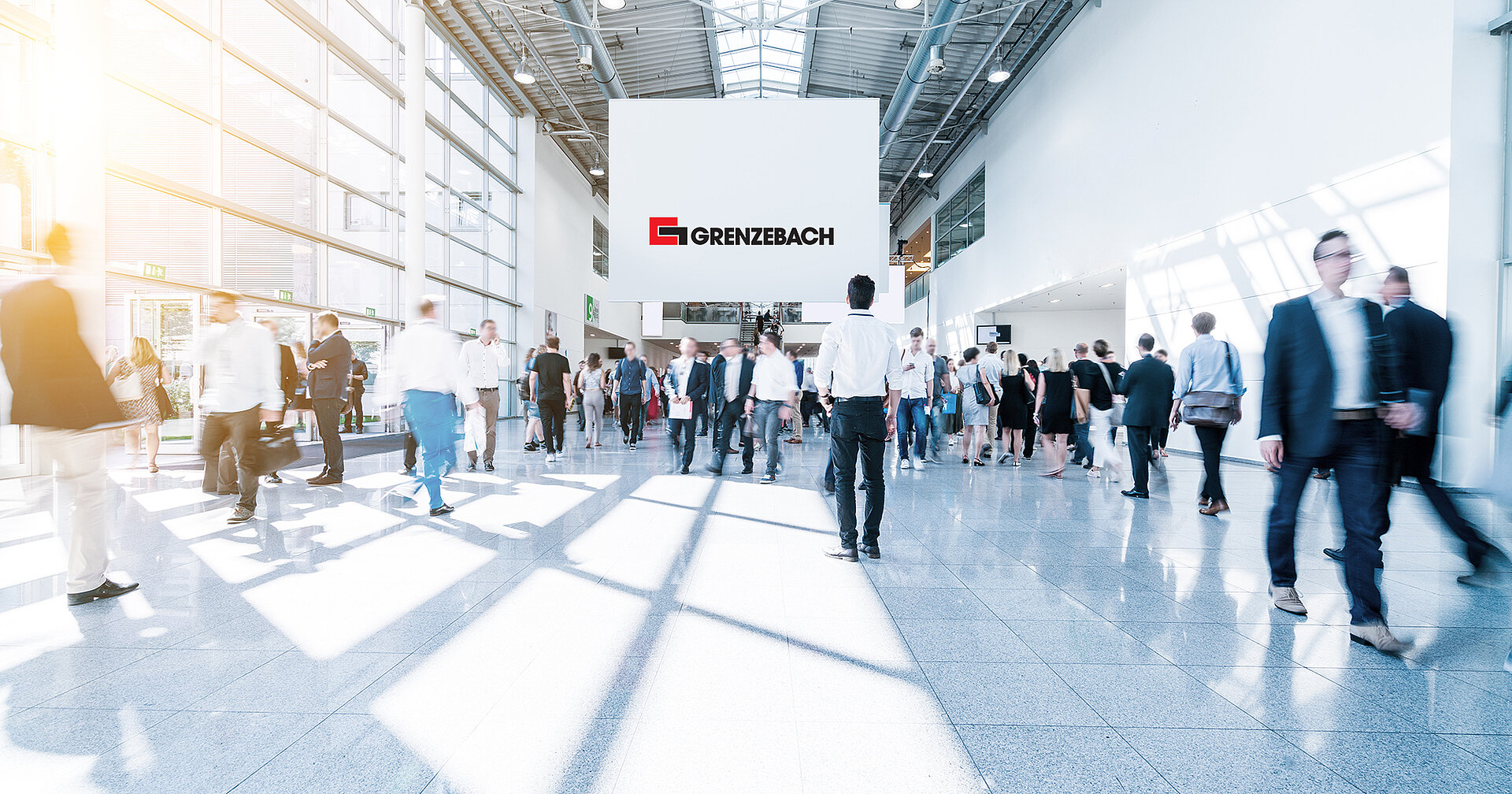
Exhibition & Events
Meet us in person or digitally
Currently, there are no events scheduled.
Use Your Potential and Contact Us Now:
Your Contact Person: Dennis Schattauer
Are you planning a new veneer drying line or would you like to optimize your veneer production? Call us or write us with your requirements. We look forward to hearing from you.
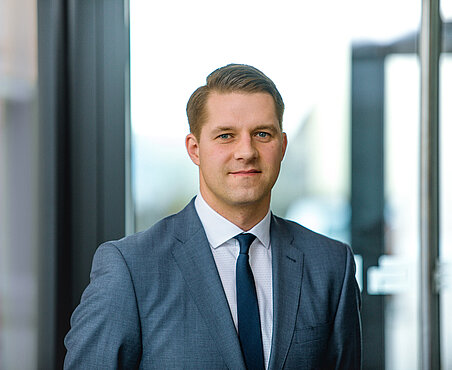