Grenzebach sends Würth products on their optimal ways
HAMLAR/ KUPFERZELL, Germany. Whether it's a work safety set for Athens, a toolbox for Vienna or a tool trolley for the 24-hour store in Waiblingen: Goods for Würth subsidiaries and shipments to customers throughout Europe are handled at the logistics center of the Adolf Würth GmbH & Co. KG in Kupferzell in the Hohenlohe district in Baden-Württemberg. The company invested around 73 million euros in the hub for the handling of bulky goods. "Logistics is a key competence at Würth. In Kupferzell, we have made the largest logistics investment in the history of the company. Grenzebach provided us with excellent support in designing and implementing an ideal concept for utilizing the new buildings," says Thomas Wahl, Logistics Managing Director at Adolf Würth GmbH & Co. KG.
Process landscape for European goods center
Grenzebach's intralogistics experts joined forces with Würth to develop the process landscape for a section of the logistics center, which opened in 2020, and supplied the required infrastructure. "It was a very exciting and rewarding task for us to co-develop the intralogistics for a new European goods center from scratch," emphasizes Martin Demharter, Project Manager at Grenzebach.
For individual warehouses to be supplied according to their specific requirements, shipments are picked accordingly. Goods from different warehouses must end up in the same shipping box. For this purpose, Würth employees load goods carriers manually or by a forklift truck at transfer stations. Grenzebach's L1200S-Li automated guided vehicles (AGVs) transport the pre-picked goods carriers from a total of 18 transfer stations to the boxing department. There, employees pack the goods into boxes at four islands, each with six packing stations. The AGVs then pick up empty goods carriers and return them to the transfer stations. Afterward, the whole process starts again.
Grenzebach fleet manager directly connected to the ERP system
Grenzebach's intralogistics solution was integrated into a huge and complex landscape of wide aisle, block and modular shelving systems. The warehouses occupy a total area with the size of eight soccer fields. Manual and automated logistics work hand in hand. The automated guided vehicle system is also digitally integrated into the Würth processes to enable that everything runs smoothly. The Grenzebach fleet manager, which controls and coordinates the vehicles, is directly connected to Würth's EWM system.
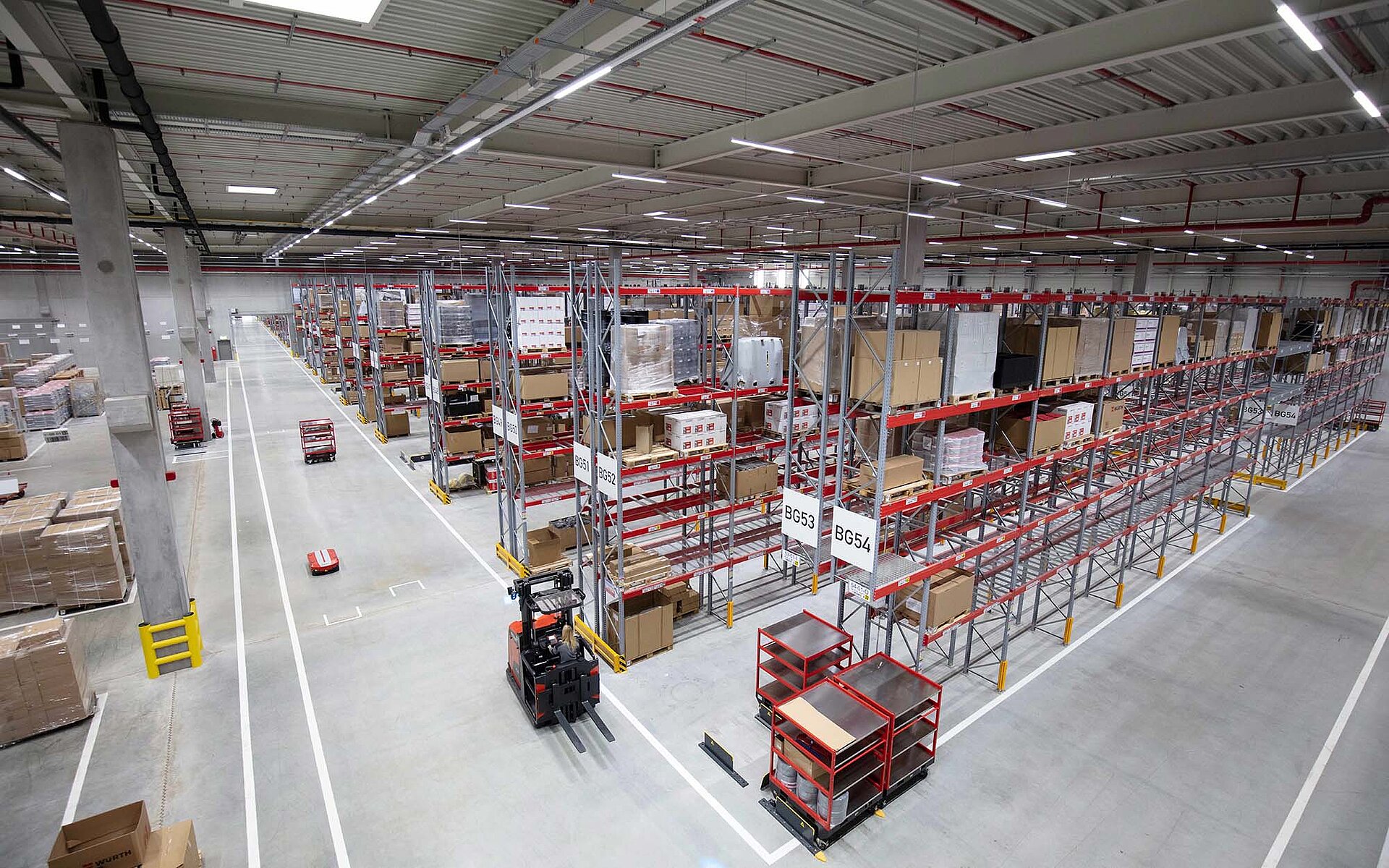
AGVs assist the logistics team
A total of around 160,000 different goods items are picked every month at the new Würth logistics center next to the A6, with individually packed deliveries being dispatched to customers all across Europe. Würth combined the transshipment points, and there are 72 docking points for trucks at the new building. "Packing parcels more efficiently to save filling material and reduce the transport volume is just as much a central goal as reducing the number of miles on the road. We combine the shipments to fewer parcels. They thus reach the customer faster and we thereby also reduce the number of truck trips by about 20 percent", Thomas Wahl explains.
To keep distances for employees as few, short and efficient as possible is an important requirement for intralogistics. This is what Grenzebach's automated guided vehicle system represents – the automated guided vehicles and the goods carriers are moving according to an integrated approach with Würth branding. Grenzebach implements a requested delivery time for empties management because time is money. A free empties space is restocked with an empties cart after ten minutes or less. "After the first few weeks, we could already see that our employees and the Grenzebach AGV interact very well," says Thomas Wahl. Alexander Gebelein, Key Account Manager at Grenzebach, adds: "One of our key objectives is that the logistics team experiences our infrastructure as a form of pragmatic, cooperative support of their work." A special feature is that, when the full goods carriers are delivered to the packing station, the AGVs initially move to a so-called "decision point" from which they are sent to the most convenient free space, depending on the workload. "This system is highly flexible and, by prioritizing accordingly, takes care that even overlapping transport orders are processed in the right order. This is a core functionality of our fleet manager," says project manager Demharter.
Personal safety and fire protection
Almost 230 employees are currently working in the 50,000-square-meter transshipment center in the Hohenlohe Industrial Park. In the final stage, there could be around 300 people working in two shifts in 2024. The Grenzebach AGVs are safe for persons. The system is in operation in two halls. The vehicles also pass fire doors on their way between the transfer stations and the boxing department. They are connected to the fire alarm system – and clear the way for the fire department in case of emergency.
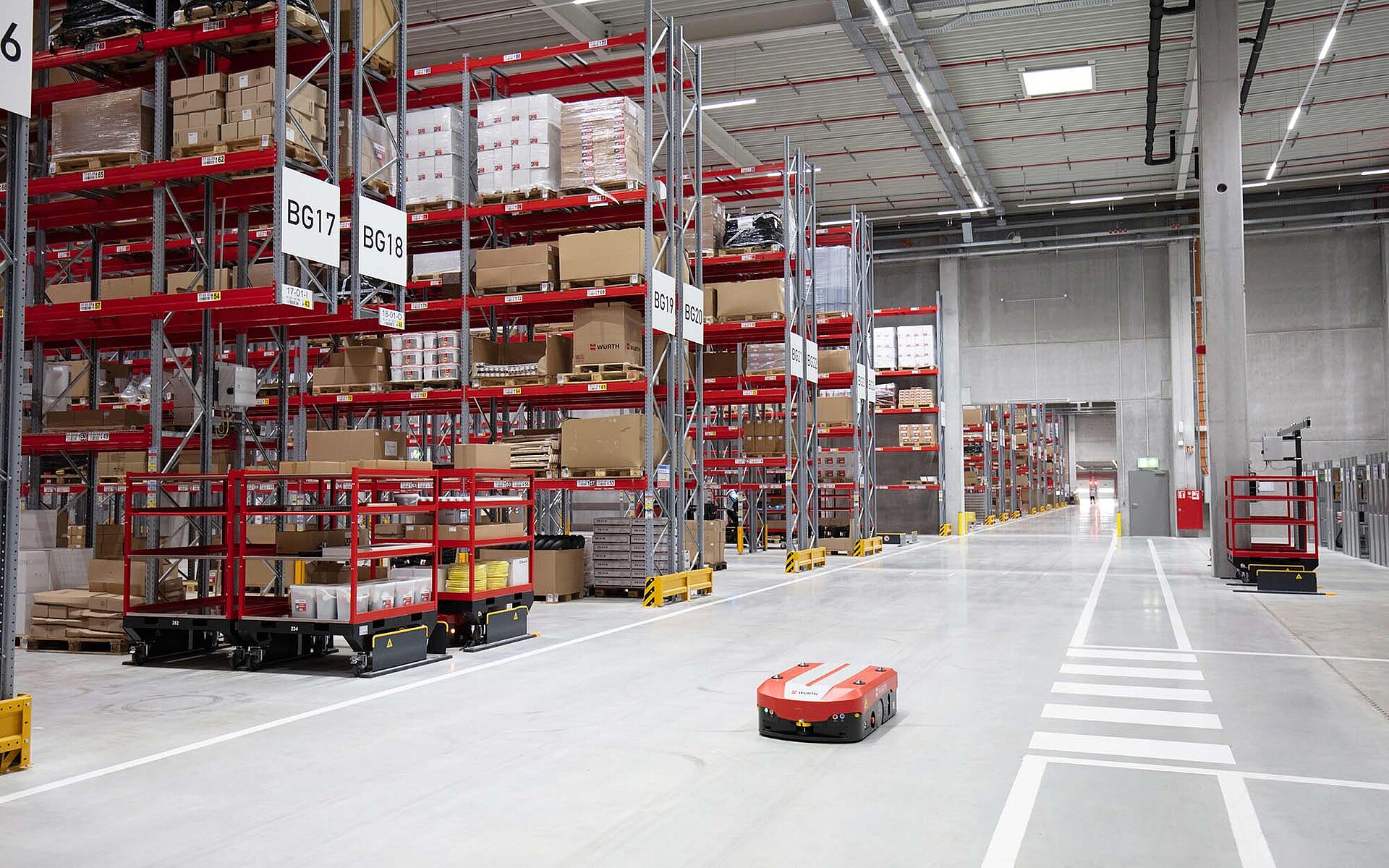
In July 2020, Würth presented the new central logistics center to the public. It had gone into operation earlier because the Grenzebach AGV had already been in use since the end of 2019. "A new building project like this involves a lot of uncertainty," says Thomas Wahl. "The processes have not yet been tested, and it is quite common that adjustments and optimizations are made after commissioning. Grenzebach supported us competently right up to the final acceptance and made individual adjustments until everything was running smoothly. Our logistics specialists and Grenzebach's intralogistics experts discussed the ideal processes in Kupferzell in the best sparring partner manner." For Alexander Gebelein and his colleagues, it was a great experience to be able to map a complex process landscape with the fleet manager and on the shop floor, as is required by a European logistics center. That includes ambitious cycle times for the provision of empty carts – a requirement that the intralogistics experts are also increasingly hearing from manufacturing companies.
Reliable, highly available and long-lasting
For Würth products to be always quickly available to customers, the intralogistics has to work reliably and seamlessly. Therefore, Grenzebach not only provides the AGV but also a comprehensive service. The system is inspected twice a year by Grenzebach technicians, and everything is thoroughly tested. In case spare parts are needed at short notice, the Grenzebach service team has prepared a small stock on-site. For major repairs, a technician is sent directly to Würth. The hotline is available for questions at any time, and Grenzebach contact persons are available by telephone around the clock for the current two-shift operation at Würth. It is also part of Grenzebach's understanding of service to provide proactive advice. "We protect our investment and invest in a long service life and high reliability of our intralogistics system from the very start with Grenzebach's service package," says Thomas Wahl.
Grenzbach has always been very flexible and solution-oriented when it came to adjustments and optimizations of the existing AGV fleet management. Improvements could already be realized during the commissioning phase and new solutions found for the internal transport of goods.