A look back into the past: The pressure is on in the workshop of the Schilde company in Bad Hersfeld. Jakob Hildebrandt and his workmates in the punching shop are struggling to keep up - so many parts are needed for industrial fans and drying systems. Today, a century later, Jakob Hildebrandt's great-grandson, Carsten Burkert, is busy dimensioning wood veneer dryers. "My great-grandfather Jakob was a foreman in the punching shop, my grandfather Rolf worked as a clerk at the company, and the positions held by my father, Bernd, included that of a technician and a project manager in the wood processing technology department." The Burkert family has been linked with the company throughout its history: from Schilde via Babcock BSH to Grenzebach BSH today.
Meeting specific challenges, enjoying diversity
After graduating from secondary school, Carsten Burkert was keen on doing a job where practical skills are needed; today he has an area of 400 square metres in total to put things into practice. That is the size of the Grenzebach BSH Technology Center where, among other things, raw materials are analysed and technological processes tested and evaluated. The Technology Center stands for 400 square metres of added competitive benefit. The 48-year old is in charge of the mechanical equipment there. Together with the nine R&D engineers and the electrician at the Grenzebach location in the German state of Hesse he sees to it that the small-scale machines and prototypes developed in the Technology Center will finally be running as full-scale systems at the customers' facilities, serving their specific needs and requirements. Activities cover a wide range: process equipment and apparatus, production plants for building materials, such as gypsum, and dryers for wood veneer are among the types of equipment the specialists in Bad Hersfeld deal with. "If a customer wants a duct routed from C to D instead of A to B, I take care of the planning and design of the modification as well as the manufacture and installation of the parts," says Carsten. "There are always new tasks, and different skills are needed for the various jobs. I like this diversity very much."
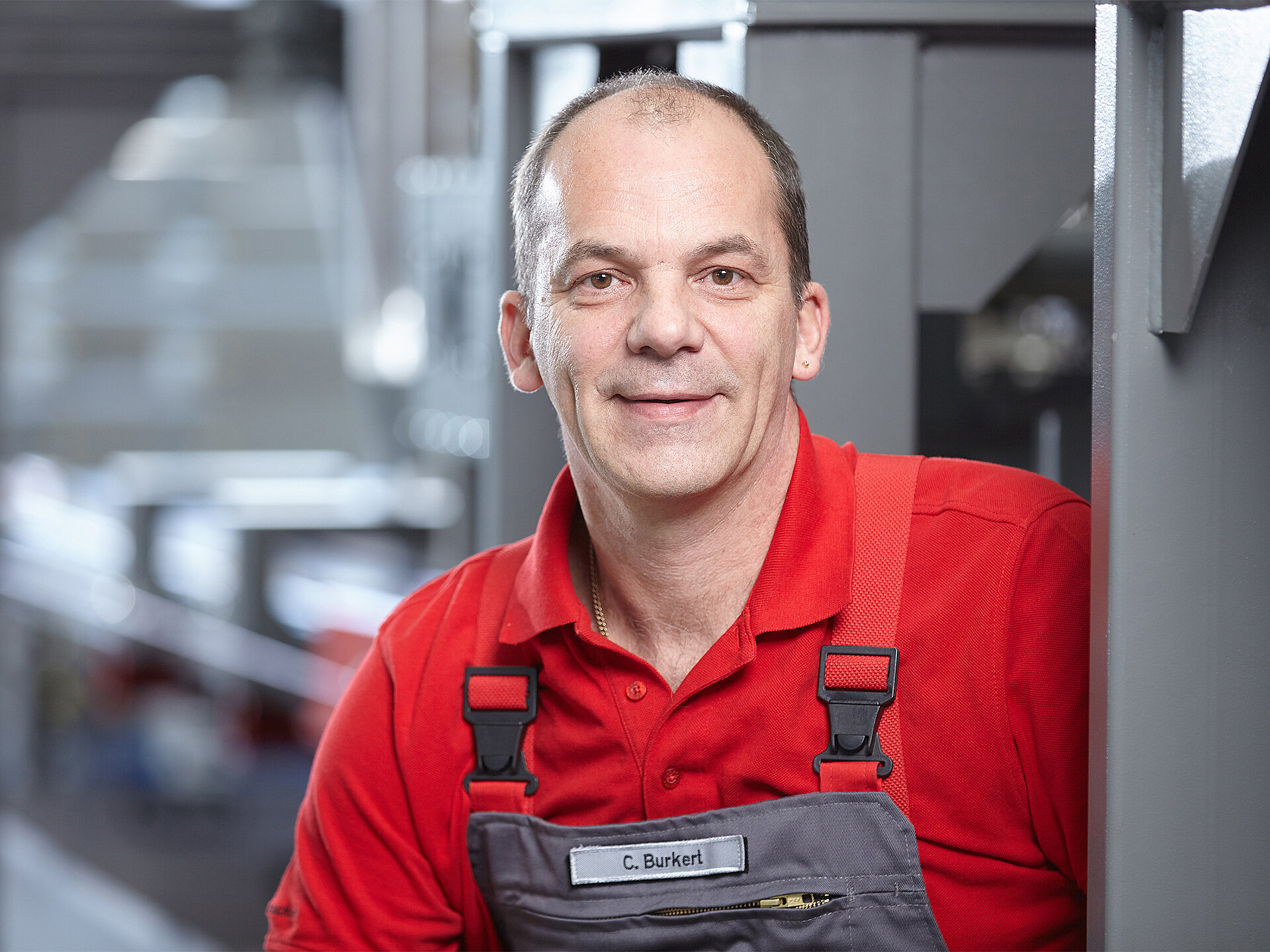
A passion for wood
One of the many practical challenges faced at the Technology Center is to help customers in the wood processing industry solve tricky problems, such as drying beech or poplar veneer, which has a tendency to become wavy, in such a way that it remains flat and smooth. The team in Bad Hersfeld has solved the problem with a special belt dryer for the customer. Wood! When this topic comes up Carsten Burkert really shines on both a professional and an emotional level. He owns and manages a stretch of forest in the region, and made some 40 cubic metres of firewood after storm Friedrike had caused a lot of damage. "This goes into the masonry heater in our home. And of course we plant new trees in the forest. Managing my forest on a sustainable basis matters greatly to me." Wood – by far not the only raw material and topic Carsten needs to deal with at Grenzebach BSH.
Working with students
He also helps students to properly incorporate the mechanical engineering part of their research into their bachelor or master thesis, for instance. Among the latest theses was one about developing a laboratory-size fluid bed cooler for a cristobalite plant. The plant was built in Vietnam and uses silica sand as a raw material. "Drawing and designing the equipment on the computer are important steps. In my view, allowing for easy maintenance and cleaning also plays a major role," comments Carsten. He says it is great when colleagues show him photos of the full-size dryer taken during commissioning on site. From wood to cristobalite to gypsum: "We also have a small plaster plant at the Technology Center. A major topic in this field is how we can reduce the amount of water that is used - and thus the energy consumption of the board dryer. Because the water added to mix the slurry must later be evaporated again from the plasterboard. So the less water we add, the more economical is the customer's production line in the end." At the in-house laboratory, which is also part of the Technology Center, Carsten's colleagues carry out chemical analyses to look into the properties of the gypsum raw materials so that the plaster plants can be tailored to each customer's specific requirements.
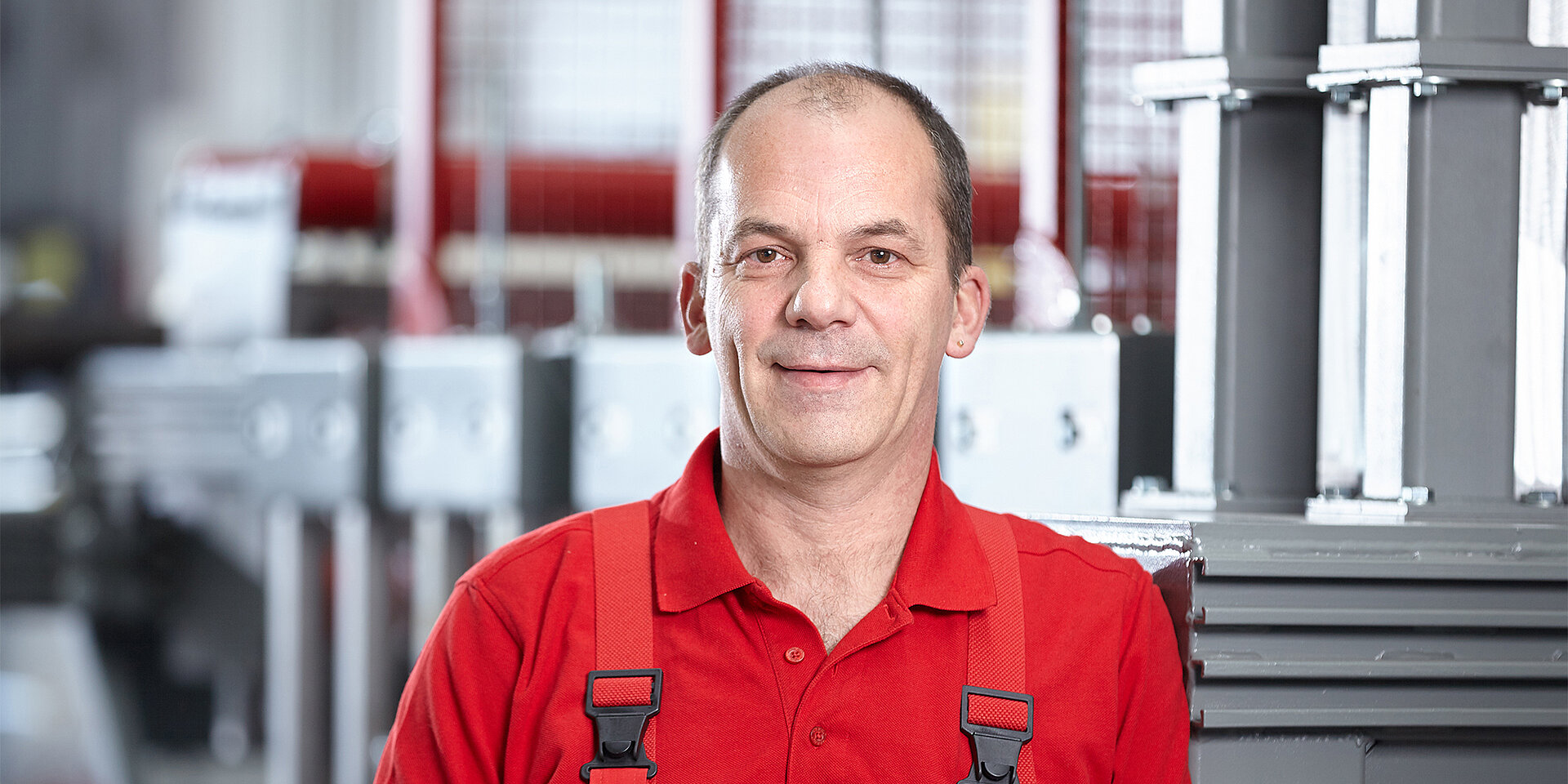
“I like working with the students. Some of them are more of a hands-on type of person, others are more gifted with computers. I find these different talents very interesting.”
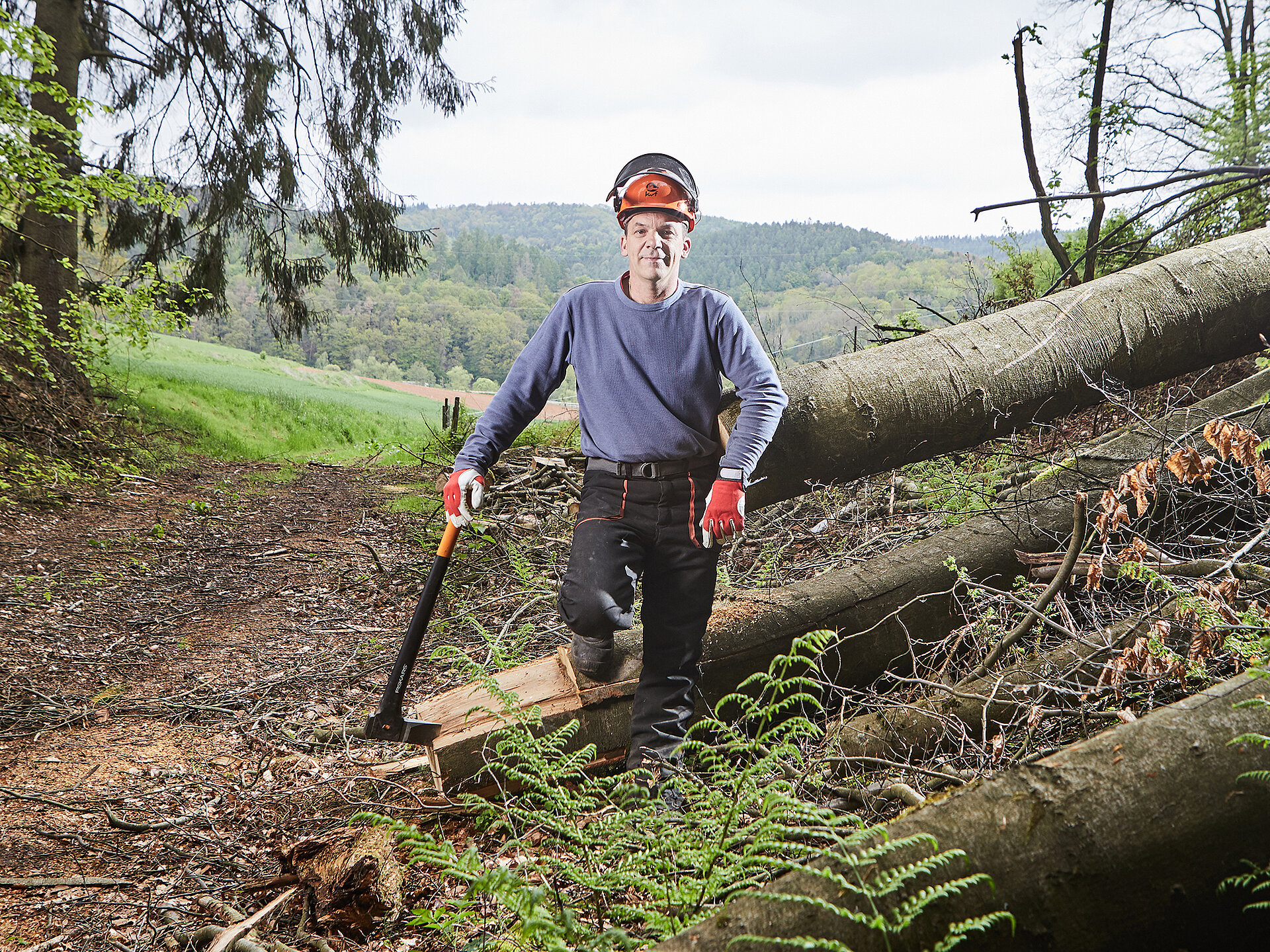