The molten glass is fed into the tin bath, which contains molten tin in an inert gas atmosphere. The glass mass spreads over the molten tin and forms a continuous ribbon. The underside of the glass floats onto tin in the tin bath and is heated from above to achieve a distortion-free and exceptionally high-quality glass ribbon and planarity on both sides. In the tin bath, the temperature of the glass drops from 1,050 degrees Celsius or 1,922 Fahrenheit at the inlet to around 600 degrees Celsius or 1,112 degrees Fahrenheit at the outlet and the glass ribbon leaves the tin bath in a formed and pre-hardened condition.
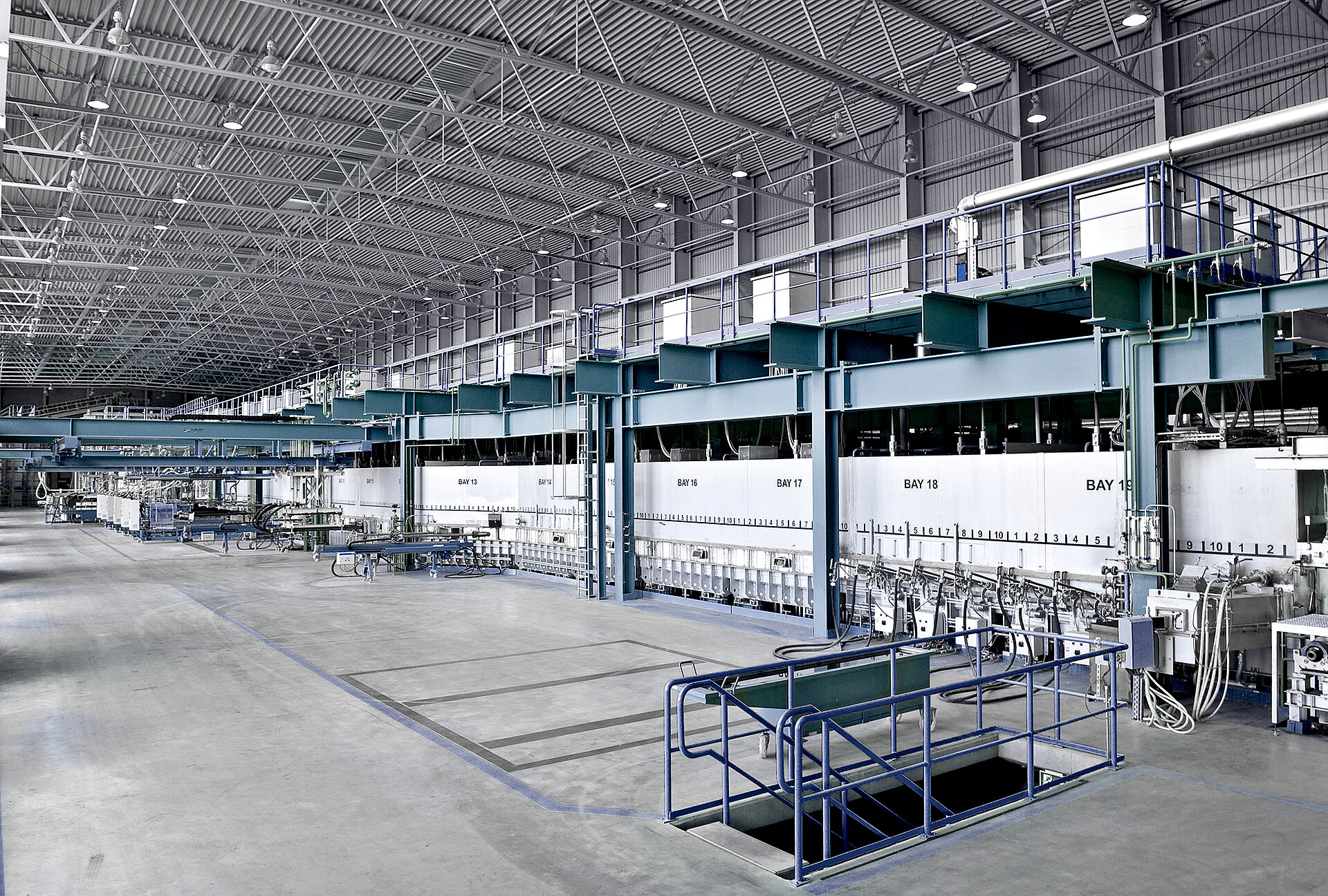
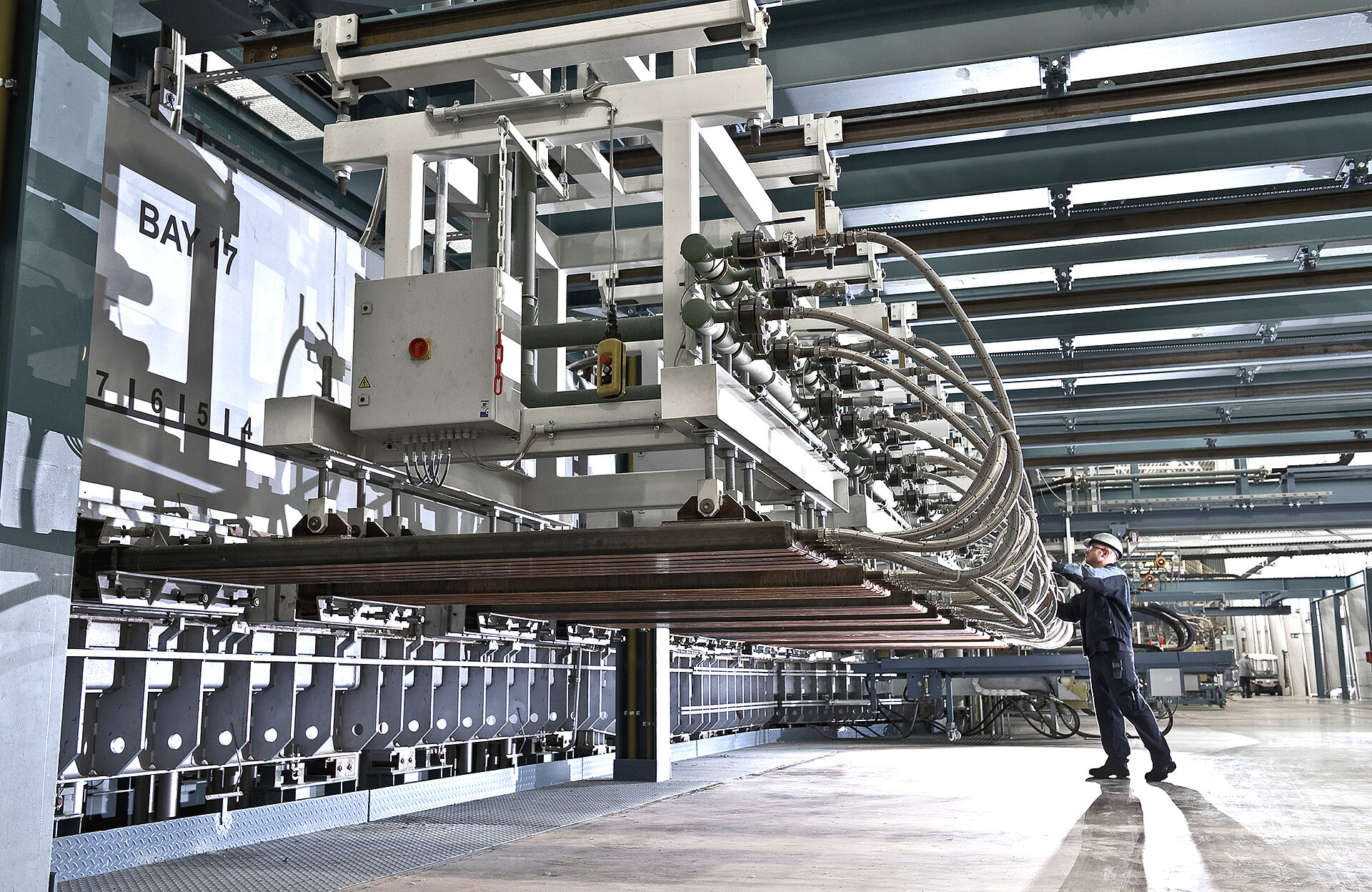
Get All Your Components From One Supplier
Tin bath equipment
Grenzebach delivers the complete tin bath with everything that goes with it. In addition to design and construction, this includes intelligent equipment combination to ensure optimal plant operation. All components of the plant are manufactured in-house. Quality-relevant plant components such as the roof, dross box, venting and de-drossing pocket have been further developed on the basis of process simulations in order to optimize the tin bath’s overall efficiency.
Tin Bath
This is how we plan and design a tin bath: you tell us the desired glass composition, the thicknesses and the tonnage; we will advise you accordingly and develop a tin bath that exactly meets your needs. In concrete terms, that means:
- Individual design based on the desired viscosity curve of the glass.
- The tin flows are analyzed in advance and optimized by means of different refractory material and graphite barrier structures – all for the highest glass quality.
- Individual tin bath bottom profiles can be developed on the basis of our simulation to avoid any flaws in the optical glass quality.
In addition to tin baths for standard glass applications in the automotive industry and architecture, Grenzebach also offers special solutions for high-temperature glasses such as high-aluminum or borosilicate glasses.
Tin Bath Roof
The tin bath roof completes the tin bath; it seals it and generates overpressure in the tin bath to shield the process from the outside world. Among other things, this is where the uniform temperature distribution is determined, which is a critical factor for optimal glass production. In addition, the protective gas is fed in to reduce atmospheric contamination and prevent defects in the glass.
EFCO, which is now part of Grenzebach, was a supplier from the very beginning: the British company Pilkington – one of the world’s leading manufacturers of glass and glass products – made the float glass process market-ready in the 1960s and initially manufactured all components of the production line itself. The first external component in this process was supplied by EFCO: it was the tin bath roof. Since then, this important process component has been continuously optimized. This knowledge base contributes significantly to Grenzebach and CNUD EFCO’s all-round expertise.
De-Drossing Pocket (DDP)
The de-drossing pocket at the end of the tin bath prevents dross from sticking to the underside of the glass ribbon while it is being lifted out of the tin bath toward the dross box. It is mounted laterally to remove the dross that accumulates in the outlet area.
The contaminated tin is passed through a refractory channel. The dross floating on the tin gets stuck on a weir, is dammed up and can be removed. The system is usually driven by a linear motor that generates electromagnetic fields and thus a flow in the direction of the de-drossing pocket. Alternatively, a paddle system can be used, which reduces the cooling effect in the process – important in the production of special glass where cooling inputs must be avoided.
Together with the dross box, it contributes immensely to the quality of the glass.
Dross Box
The dross box is the interface and sluice between the tin bath and the annealing lehr. Here, for the first time, the glass floating on the tin is lifted out by three motorized rollers and transferred to the annealing lehr. The dross box also has the important task of sealing the tin bath atmospherically. This is done by means of graphite pressing below the driven rollers and curtains above the glass.
The special features of the Grenzebach dross box include adjustable pressure on the graphite blocks and an adjustable roller height. In addition, the dross box is not welded but attached by means of a clamping device, which is firmly secured after the tin bath has been heated to 620 °C. In this way, physically induced thermal expansion is taken into account without deforming the construction. Additional advantages include lower heat losses and a more homogeneous heat distribution within the dross box.
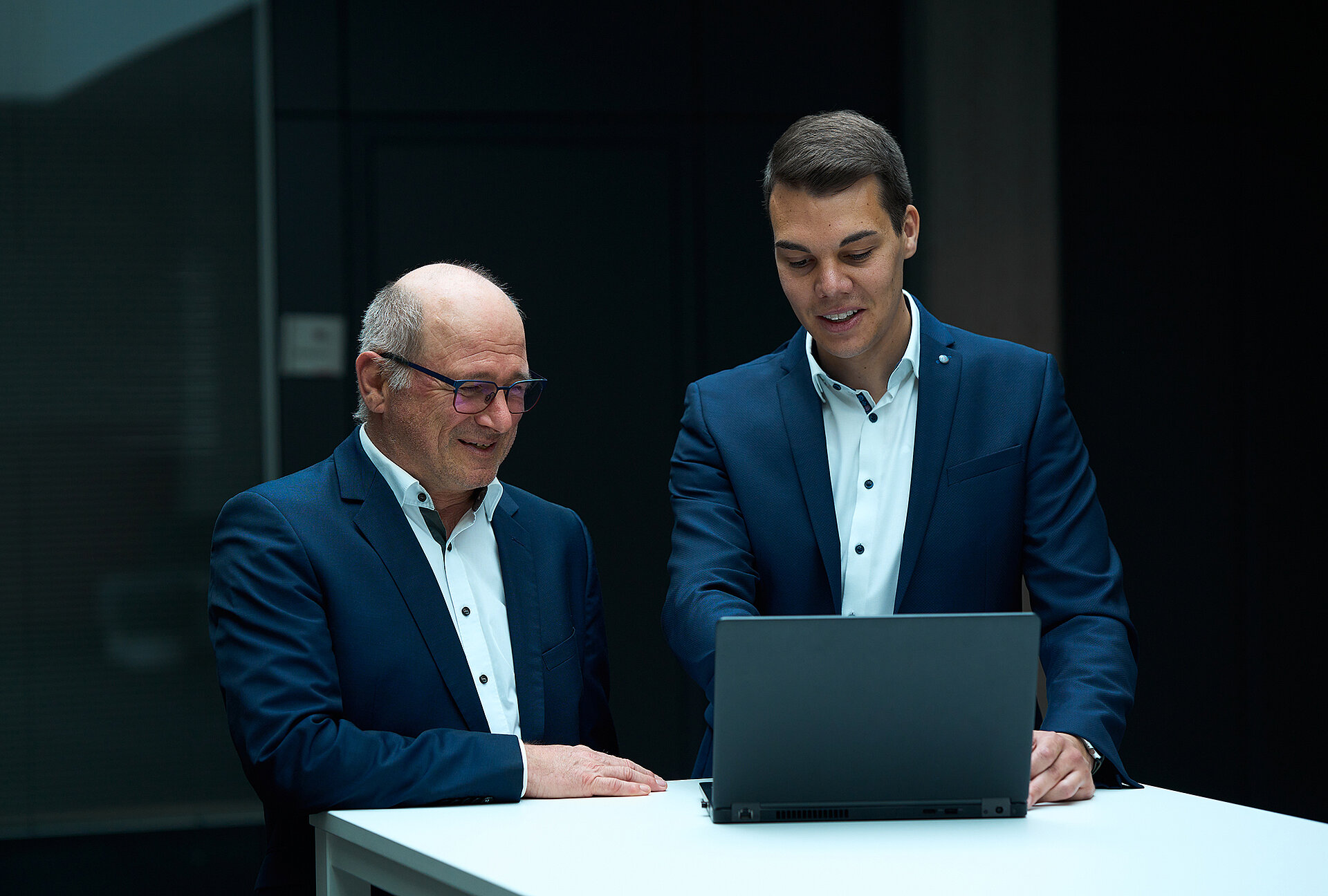
“No space is wasted: Our tin bath is 6 to 9 meters shorter than usual, as the cooling area is optimized. This enables us to offer tin baths that produce the same yield despite their compact dimensions.”
We Developed a Shorter Tin Bath That Delivers the Following Benefits:
Lower CAPEX
The compact tin bath reduces investment costs across the board. A shorter building, less steel construction, less space and less tin (10 - 15 percent): all this adds up to considerable savings
Lower OPEX
In addition to the initial investment, the consumption of resources is also reduced. Less heat loss, less inert gas required, less loss due to atmospheric leakage and less risk of errors as well as a smaller free tin surface: these are advantages you enjoy throughout the entire life cycle of the plant.
Higher Output
This allows the tonnage of the glass production line to be increased in the event of a cold repair, that is, with an existing glass plant and available space – which means that you produce more output with the same size of tin bath. We will check and individually calculate exactly what and how much is feasible in each specific case.
A 3D Design Simulation Makes a Better Variant Possible.
The dependencies of atmosphere, tin, glass and temperature in the whole tin bath can be simulated and analyzed first via a 3D design. The findings pay dividends because float bath technology is enhanced even further.
We are here for you
Your Contact Person: Markus Michels
Collaboration means dialogue. We support you no matter where you are in the world. Contact us. Send us your enquiry.
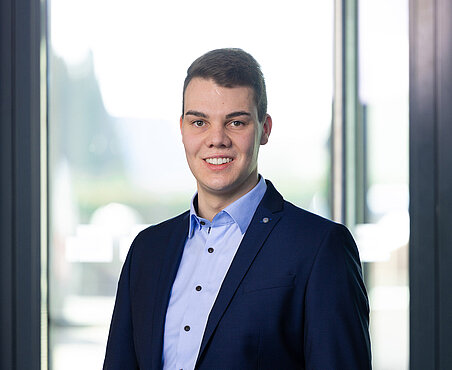