Built in record time: production line for flexible wood fiber insulation boards
The project:
Our customer:
ZIEGLER GROUP is an owner-managed business group with 34 locations and activities worldwide. It is a global player in the wood processing, house construction, logistics, mechanical engineering, gastronomy, and decoration sectors.
The challenge for the customer:
"From the tree to the house" is ZIEGLER GROUP's philosophy. The vision of building wooden houses that are 100 % ecological is something that unites all business divisions of the group and, in 2021, prompted its decision to start producing wood fiber insulation boards. On the one hand, it allows ZIEGLER GROUP to make efficient use of valuable raw materials generated at the sawmill and, on the other hand, to provide another link to the value chain by itself. To enter the booming wood fiber insulation materials market as quickly as possible, the company set an ambitious goal: in just twelve months, a state-of-the-art production line with the highest capacity on the market would be built in Hütten, Germany.
The solution:
Grenzebach took up the challenge and after a record construction time of just one year, they were able to successfully hand over the new mega-facility on schedule – even though the trade press had written that meeting the tight schedule would be virtually impossible, and with the COVID-19 pandemic creating numerous delays and causing shortages of materials and workforce. In record time, the Grenzebach specialists managed to plan and build a complete production line for flexible wood fiber insulation boards, including full installation and commissioning.
The solution package:
- The new design of the fiber blending system provides higher capacities and better blending results than existing systems.
- The curing oven is an entirely new design explicitly developed for processing wood fibers – it is a modular system with variable airflow directions for optimum board curing.
- The intelligent instrumentation and control system monitors all process steps and provides fully-automated control of the process and product optimization.
- The configuration of the production line allows quick change-over and retooling times and enables the customer to produce a wide variety of boards with different thicknesses, dimensions, and product properties.
- The entire production line is easily accessible for cleaning, maintenance, and repair to minimize downtime.
Benefits for our customer:
High availability
through the best equipment quality and minimized downtime.
Maximum sustainability
through utilization of the owner's raw materials and a climate-neutral energy supply.
Excellent efficiency
through high system flexibility and innovative production technology.
Maximum output
through a production capacity of up to 1.5 million cubic meters of flexible boards per year.
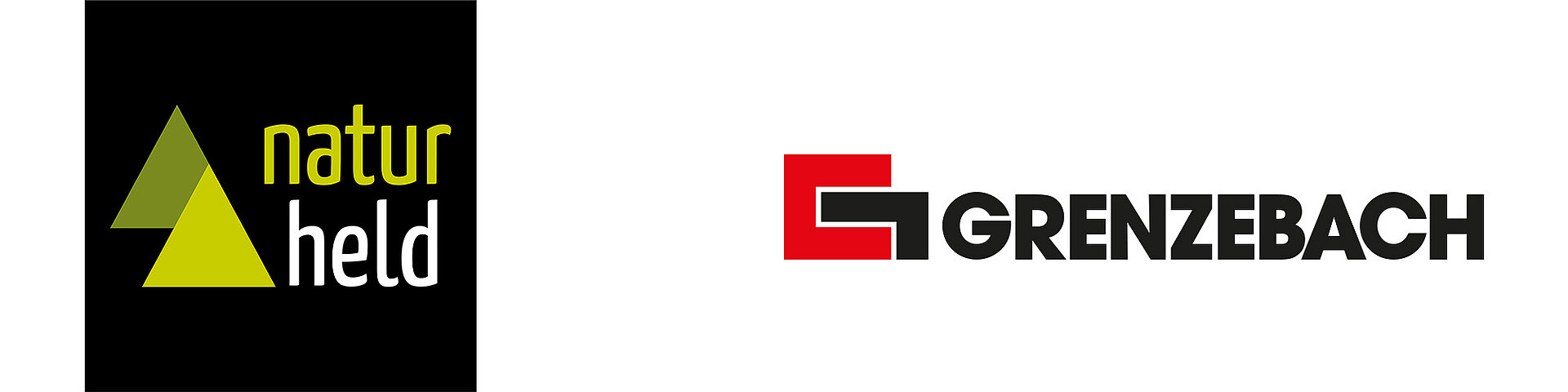
“Building the insulation board plant within such an extremely short period was possible only thanks to the close cooperation with a renowned automation partner of international standing like Grenzebach. As a solution provider, Grenzebach supplied both the product and the equipment know-how and expertise and was able to make the required capacities available at all times.”