The hidden potential of automated post-processing
- Most additively printed components require post-processing
- Automated post-processing offers greater efficiency and productivity, lower cost per part and active occupational health and safety
- Grenzebach and EOS have developed post-processing solutions for the EOS Shared Modules concept
Components manufactured using Additive Manufacturing often must be post-processed by hand – regardless of whether they are a prototype, a tool, or a final product. However, the more Additive Manufacturing (AM) is used in industrial series production, the more critical automated post-processing becomes to maintain consistent quality. Despite this, the post-processing phase is often not considered when purchasing a 3D printer, even though this essential process step accounts for nearly 47 percent of a company's manufacturing costs, according to PostProcess' 2nd Annual Post-Printing Trends Report. "This has to change," says Mario Schafnitzel, Product Manager Additive Manufacturing at Grenzebach, "because only companies that also automate post-processing in serial production can remain competitive and marketable in the long term." But how can post-processing be intelligently automated?
Harnessing hidden potential of post-processing
Most additively printed components require post-processing. These can be simpler processes such as substrate removal, sorting, or coloring; or more complex processes such as inspecting the part geometry, heat treatment, or part sorting.
A unique automation solutions can reduce manual interventions to a minimum, reduce costs and sustainably increase productivity. "However, post-processing in particular still has the lowest level of automation compared to the pre-processing and printing phases," explains Mario Schafnitzel, "although in our opinion this is where the greatest cost-benefit leverage lies."
For this reason, Grenzebach and EOS have developed solutions for the EOS Shared Modules concept that automates the next process steps after the build job has been finished. The solution includes, among others, the steps of unpacking, de-powdering and setup. Companies can implement the concept holistically or just the individual components – depending on their needs and wishes.
Three reasons for automating post-processing
1. Greater efficiency and productivity
If companies automate post-processing, the different throughput times that occur in printing and pre/post-processing can be intelligently and reliably coordinated. This enables companies to achieve optimum production flow and maximum output.
2. Lower costs per part
Companies make maximum use of their equipment by intelligently networking the individual work steps. As a result, they produce at lower costs per part.
3. Active occupational health and safety
During the post-processing of 3D printed components, health risks may exist due to fine dust and nanoparticles. With Grenzebach automation solutions, companies comply with occupational health and safety regulations and reduce employee risks as well as costs for technical protective measures and personal protective equipment.
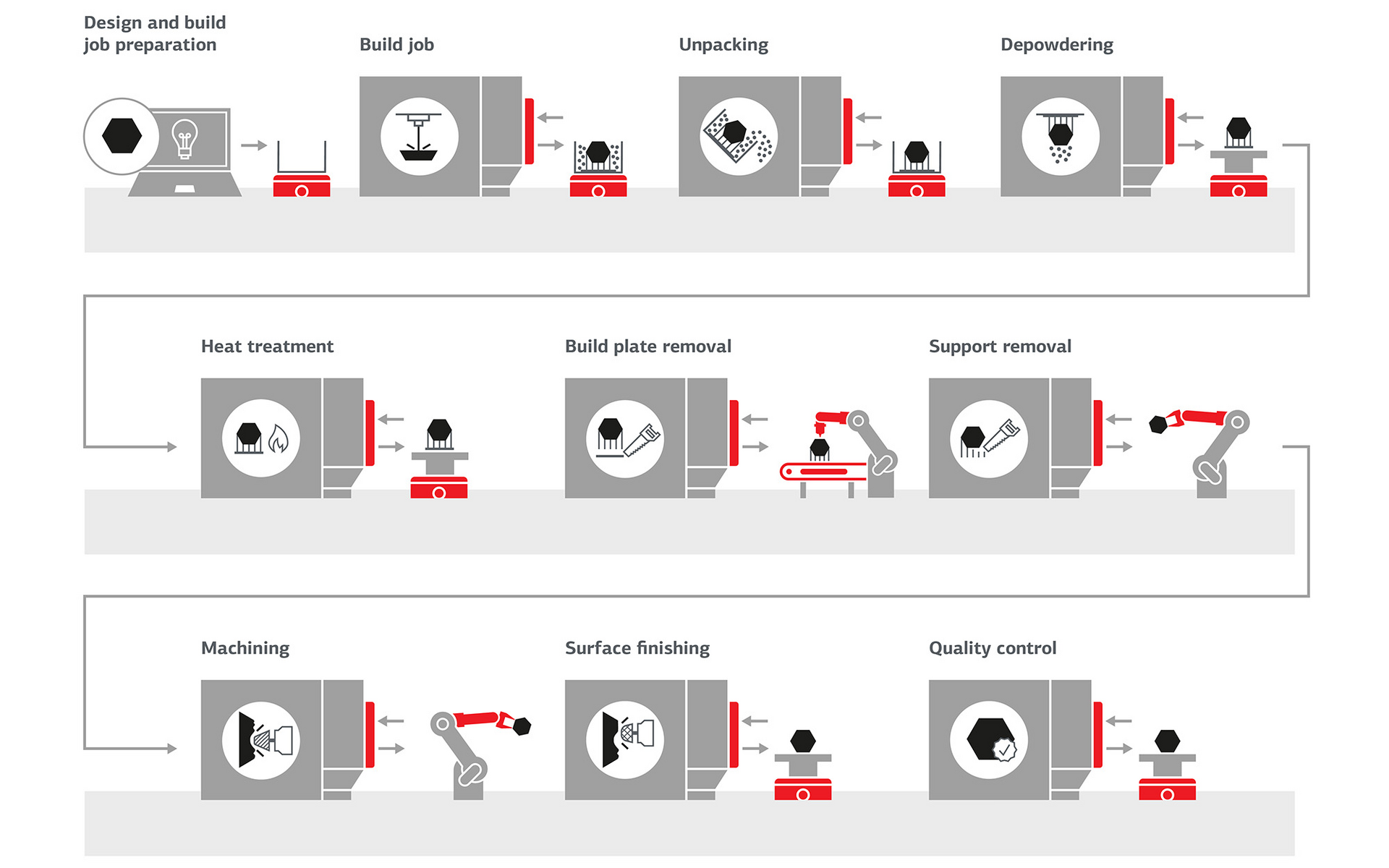
Successfully mastering the leap into automation – with the right partner.
For a successful lights-out factory, it is crucial to intelligently network the process steps of Additive Manufacturing from start to finish. As an experienced automation partner to numerous industries and a full-service provider, Grenzebach is a reliable partner for the leap into full automation for powder-based Additive Manufacturing. Grenzebach's automation technology is independent of the printing technology used and can be implemented in both new and existing systems. With locations in five time zones, Grenzebach implements solutions for companies worldwide. Customers also benefit from individual solutions and holistic automation concepts. The automation equipment can also be tailored to individual requirements and includes:
- AGVs and goods carriers
Automated guided vehicles make processes more flexible in the long term. Depending on requirements, suitable goods carriers are used open or closed (with/without inert gas).
- Machine Fitting
Grenzebach develops, designs, and builds interfaces for existing equipment, such as airlocks or attachments. In this way, the company enables an efficient and safe automated process.
- Robot cells
Gripping, removing, inspecting – Grenzebach implements the complete range of stand-alone solutions up to the 7th axis and integrates robots from different manufacturers.
- Transport and handling technology
Permanently installed conveyor lines supplement driverless transport systems if required. Material is delivered in time; components are transported individually or on the building platform.
- Inspection solutions
Grenzebach inspects the quality of the produced components inline or outline via 2D/3D image processing systems directly in the process chain – including part recognition and sorting.
- Software Integration
The 3D printing process, including upstream and downstream areas, is digitally mapped and controllable.
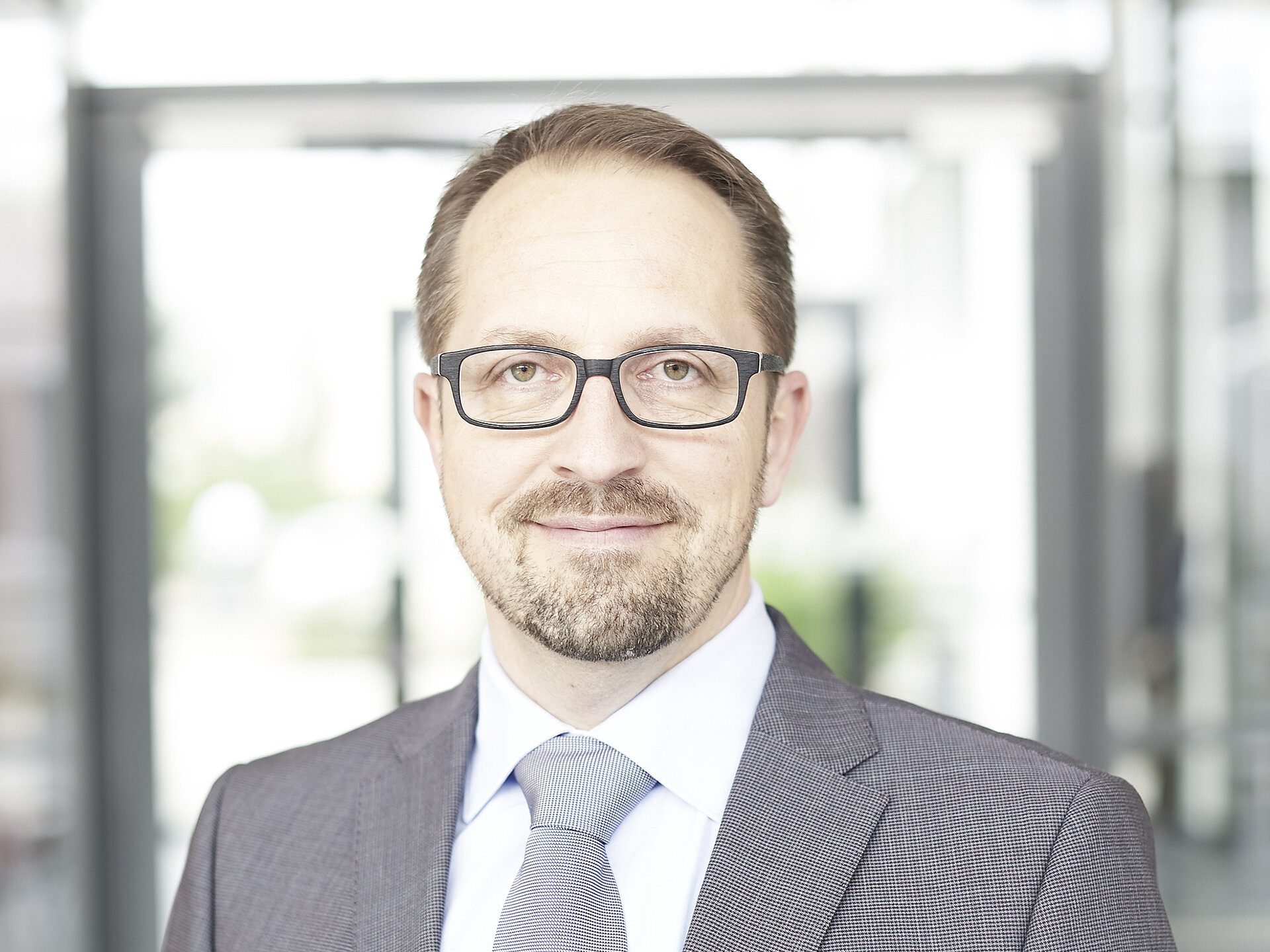